Mastering the Basics: A Beginner's Guide to Control Valves
On this page
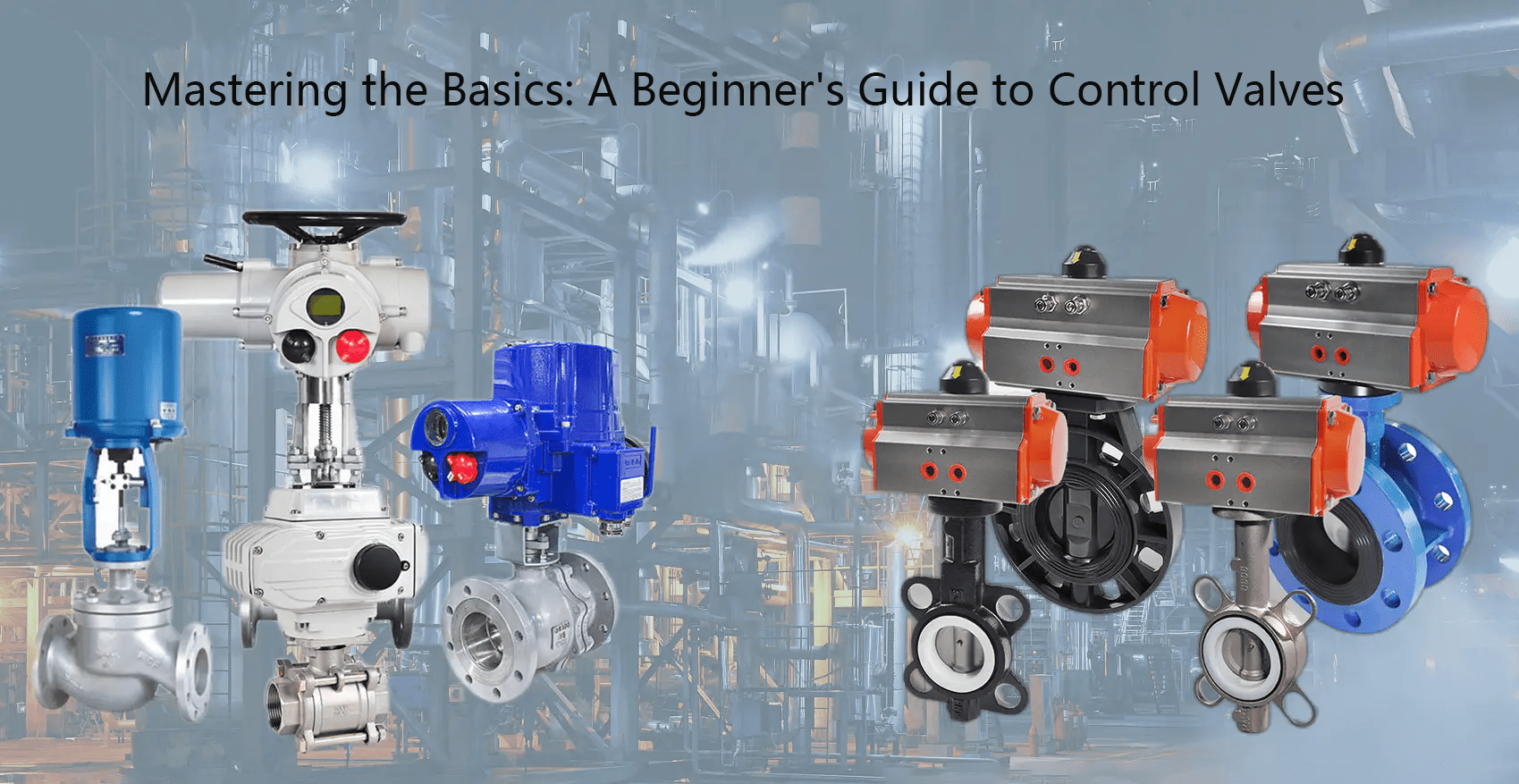
Control valves are omnipresent in industrial settings, yet their intricacies often elude understanding. This guide navigates through their fundamentals, shedding light on their definition, functionality, applications, types, and inherent advantages and disadvantages. A control valve is a mechanical device designed to regulate the flow, pressure, or temperature of a fluid within a system. It achieves this by varying the size of the flow passage through the valve in response to signals from a controller. By modulating the flow of fluid, control valves maintain process parameters within desired limits, ensuring efficient system operation. Control valves operate based on the principle of altering flow resistance. The valve's position is adjusted to either restrict or permit fluid flow, thereby controlling process variables. This adjustment is facilitated by an actuator, which receives signals from a controller and translates them into mechanical movement. As the actuator moves, it adjusts the valve's position, modulating flow according to system requirements. Control valves find extensive application across various industries, including oil and gas, chemical processing, power generation, water treatment, and HVAC systems. They are utilized in processes such as flow control, pressure regulation, temperature control, and fluid mixing. From controlling steam flow in power plants to regulating chemical processes in refineries, control valves play a crucial role in ensuring optimal system performance. Control valves are categorized based on their design and function, with common types including globe control valves, butterfly control valves, ball valves, and diaphragm valves. Globe valves offer precise flow control and are suitable for throttling applications. Butterfly valves provide excellent flow modulation in large pipelines, offering low pressure drop and reduced maintenance requirements. Ball valves offer quick and reliable on/off control, while diaphragm valves are ideal for applications requiring clean and sterile conditions. Control valves offer several advantages, including precise control over process variables, flexibility in operation, and compatibility with various control methods. They enable automation, enhancing system efficiency and reducing manual intervention. However, control valves also have limitations, such as susceptibility to wear and tear, potential for leakage, and complexity in maintenance and repair. Additionally, improper selection or installation can lead to inefficiencies or system failures. Understanding the basics of control valves is essential for engineers, technicians, and anyone involved in industrial processes. By grasping their definition, functionality, applications, types, and pros and cons, stakeholders can make informed decisions regarding valve selection, installation, and maintenance. As control valves continue to evolve with advancements in technology, mastering their fundamentals remains pivotal for optimizing system performance and achieving operational excellence.