How Does a Globe Control Valve Work?
On this page
A globe control valve is a crucial component in many industrial systems, used for regulating flow and ensuring smooth operations. Understanding its functionality is essential for anyone involved in industrial processes or mechanical engineering. Here’s an in-depth look at how a globe control valve works, its components, and its applications.
A globe control valve is named for its spherical body shape, although the internal structure is more complex. These valves are designed to start, stop, and regulate fluid flow in a pipeline. The key feature that distinguishes globe valves from other types is their flow regulation capability, which is achieved through a movable plug or disc and a stationary ring seat within a typically spherical body.
The main casing that houses all internal components. It must withstand the pressures and temperatures of the fluid it regulates.
Attached to the valve body, the bonnet covers the moving parts of the valve and can be removed for maintenance.
This movable element adjusts to regulate the flow. When the valve is open, the plug is lifted off the seat, allowing fluid to pass. When the valve is closed, the plug is seated firmly against the ring seat, stopping flow.
The stationary component that the plug presses against to stop flow.
A rod that connects the actuator to the plug. It moves the plug up or down based on the actuator’s input.
The mechanism that moves the stem and plug. Actuators can be manual (handwheel), pneumatic, electric, or hydraulic.
The operation of a globe control valve involves several steps:
The actuator receives a signal, often from a process controller, indicating the required position of the valve plug.
Depending on the actuator type, the stem moves vertically. In manual valves, this is done by turning a handwheel, while in automated systems, the actuator performs this action.
As the stem moves, it adjusts the position of the plug relative to the seat. Lifting the plug off the seat opens the valve, allowing fluid to flow through. Lowering the plug closes the valve, blocking the flow.
Intermediate positions of the plug between fully open and fully closed allow for precise regulation of the flow rate. This modulation is what makes globe control valves particularly useful in applications requiring fine control.
Globe valves come in various types, each suited for specific applications:
The most common type, with a simple Z-shaped flow path that offers moderate resistance to flow.
Designed for high-pressure applications, this valve has an angled stem to reduce flow resistance and provide smoother operation.
Useful where space is limited, as it changes the direction of flow by 90 degrees.
Globe control valves are versatile and used in numerous industries:
Oil and Gas: For regulating the flow of hydrocarbons and other fluids in pipelines and refineries.
Chemical Processing: To manage the flow of various chemicals in manufacturing processes.
Power Generation: In steam and water systems within power plants.
Water Treatment: For controlling the flow of water and treatment chemicals.
HVAC Systems: To regulate heating and cooling fluids. Advantages:
Precise Flow Control: The ability to modulate flow rates accurately makes them ideal for fine control applications.
Durability: Sturdy construction materials ensure long service life.
Versatility: Suitable for a wide range of temperatures and pressures.
Disadvantages:
Flow Resistance: The tortuous path of the fluid can cause significant pressure drops.
Size and Weight: Generally heavier and bulkier compared to other valve types.
Maintenance: More moving parts mean potentially higher maintenance requirements. Understanding how a globe control valve works is essential for optimizing industrial processes. These valves offer precise control over fluid flow, making them invaluable in many applications. Despite some disadvantages, their benefits often outweigh the drawbacks, particularly where accurate flow regulation is critical. By carefully selecting the right type and maintaining it properly, industries can ensure efficient and reliable operation of their systems.
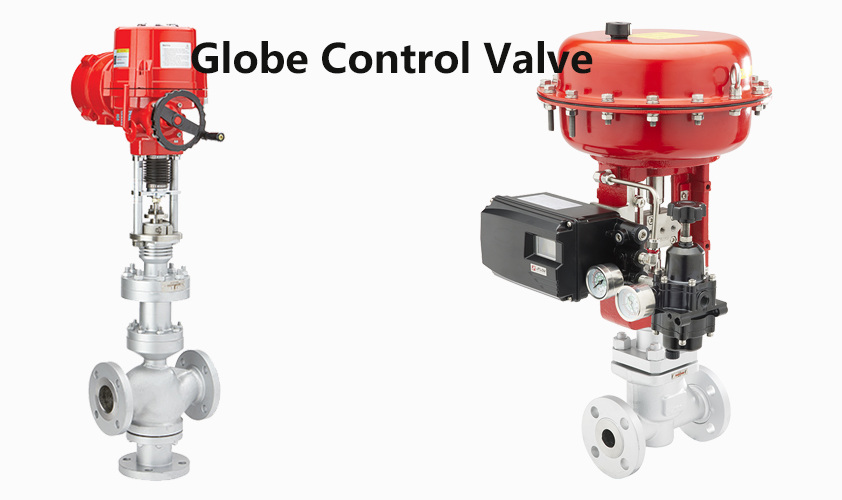
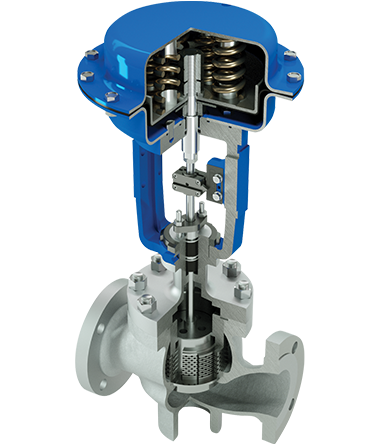
Oil and Gas: For regulating the flow of hydrocarbons and other fluids in pipelines and refineries.
Chemical Processing: To manage the flow of various chemicals in manufacturing processes.
Power Generation: In steam and water systems within power plants.
Water Treatment: For controlling the flow of water and treatment chemicals.
HVAC Systems: To regulate heating and cooling fluids. Advantages:
Precise Flow Control: The ability to modulate flow rates accurately makes them ideal for fine control applications.
Durability: Sturdy construction materials ensure long service life.
Versatility: Suitable for a wide range of temperatures and pressures.
Disadvantages:
Flow Resistance: The tortuous path of the fluid can cause significant pressure drops.
Size and Weight: Generally heavier and bulkier compared to other valve types.
Maintenance: More moving parts mean potentially higher maintenance requirements. Understanding how a globe control valve works is essential for optimizing industrial processes. These valves offer precise control over fluid flow, making them invaluable in many applications. Despite some disadvantages, their benefits often outweigh the drawbacks, particularly where accurate flow regulation is critical. By carefully selecting the right type and maintaining it properly, industries can ensure efficient and reliable operation of their systems.