What Happens When Solenoid Control Valve Goes Bad?
On this page
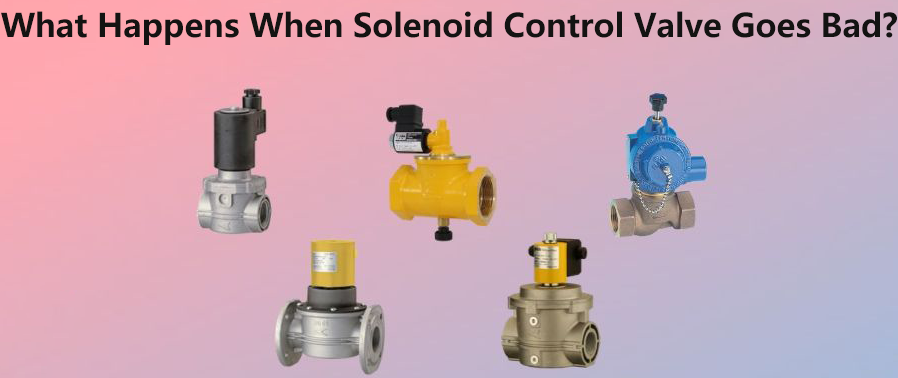
When a solenoid control valve malfunctions, the repercussions can be significant and far-reaching. These valves play a crucial role in various industrial and mechanical systems, regulating the flow of fluids and gases with precision. Understanding the effects of a defective solenoid valve is essential for maintaining operational efficiency and preventing potential hazards. Solenoid control valves are integral components in numerous applications, from hydraulic and pneumatic systems to HVAC equipment and automotive engines. These valves utilize electromagnetic energy to control the movement of fluids or gases through pipes and conduits. When functioning correctly, they ensure precise flow control, facilitating the smooth operation of machinery and processes. Identifying the early signs of a failing solenoid control valve is crucial for preemptive maintenance and avoiding operational disruptions. Common indicators include: Visible leaks around the valve or within the system indicate potential valve failure. This can lead to fluid loss, pressure drops, and environmental contamination. Inconsistent or erratic fluid flow patterns suggest internal valve malfunction, affecting system performance and efficiency. The inability of the valve to open or close as commanded disrupts flow control, impacting the functionality of connected equipment. Unusual noises or vibrations during valve operation may signify internal wear, misalignment, or impending failure. In industrial settings, the failure of a solenoid control valve can have profound effects on production and safety: Equipment reliant on accurate fluid or gas flow may experience downtime, resulting in decreased productivity and potential financial losses. Variations in fluid flow due to valve malfunction can compromise product quality and consistency, affecting manufacturing standards. Improper valve operation can lead to unsafe conditions, such as pressure build-up, overheating, or equipment damage, posing risks to personnel and facilities. Within mechanical systems, such as automotive engines or HVAC units, the consequences of a faulty solenoid control valve are equally impactful: In automotive applications, malfunctioning valves can cause engine misfires, decreased fuel efficiency, and emission control issues. Faulty valves in HVAC systems may lead to inadequate heating or cooling, temperature fluctuations, and increased energy consumption. Beyond operational disruptions, a malfunctioning solenoid control valve can have environmental and economic implications: Leaking valves can release harmful fluids into the environment, necessitating cleanup efforts and potentially causing regulatory compliance issues. Addressing valve failures involves repair expenses and downtime-related costs, impacting overall operational budgets. To mitigate the risks associated with solenoid control valve failures, proactive maintenance and monitoring are essential: Implement scheduled inspections to detect early signs of wear, corrosion, or mechanical stress. Periodic analysis of fluid quality and composition can reveal contaminants or irregularities that may affect valve performance. Educate personnel on the importance of proper valve operation, maintenance procedures, and safety protocols. The impact of a faulty solenoid control valve spans across industrial, mechanical, environmental, and economic domains. Recognizing the signs of valve deterioration, understanding its consequences, and implementing preventive measures are critical for maintaining operational efficiency and safety. By prioritizing proactive maintenance and investing in quality components, industries can minimize downtime, enhance productivity, and uphold environmental stewardship. As technology advances, the evolution of solenoid control valves continues to improve efficiency and reliability. Innovations in materials, design, and predictive maintenance techniques promise to further enhance valve performance and longevity, supporting sustainable industrial practices and operational excellence.
In conclusion, while the consequences of a faulty solenoid control valve are significant, proactive measures and advancements in valve technology offer pathways to mitigate risks and optimize system performance in various applications.