What is a Modulating Control Valve?
On this page
A modulating control valve is an essential component in many industrial processes, designed to regulate the flow of fluids by opening, closing, or partially opening. Unlike on-off valves that are either fully open or fully closed, modulating valves offer the ability to precisely control flow, ensuring that the process operates efficiently and within specific parameters. Typically automated with the help of an actuator, these control valves are widely used to manage the flow rate of liquids, gases, or steam in various systems.
Modulating control valves are crucial for maintaining process stability, especially in systems where factors like temperature, pressure, or fluid levels need to be carefully monitored and controlled. The feedback system integrated into these valves communicates with the operator or control system, allowing real-time adjustments to be made. Common modulating control valves include globe valves, disc valves, and quarter-turn valves such as butterfly and ball valves. With their ability to fine-tune flow, these valves are vital to numerous industries including HVAC, chemical processing, and water treatment. Modulation refers to the ability of a valve to adjust its position between fully open and fully closed to regulate the flow of a medium. Unlike conventional valves that only provide an open or closed state, modulating valves control the degree of openness, allowing for a more precise and continuous regulation of flow. This is crucial for processes where the exact flow rate needs to be maintained over time, rather than simply being turned on or off.
Modulating control is often used to manage secondary variables, such as temperature, pressure, or the level of fluid in a tank. For instance, in a heating system, a modulating valve can control the flow of hot water to maintain a specific room temperature. In industrial processes, modulating valves are used to control the flow of chemicals, steam, or gases to ensure precise conditions are met. This fine-tuned control helps improve efficiency, reduce energy consumption, and ensure product quality.
There are several types of modulating control valves, each suited to specific applications and operational requirements:
Globe valves are one of the most commonly used types of modulating control valves. They are designed with a spherical body and an internal baffle that divides the valve into two halves. The position of the valve disc controls the flow rate. Globe valves are preferred in applications that require throttling and precise flow control. Their ability to regulate flow makes them ideal for systems where accurate modulation is required, such as in heating and cooling systems.
Ball valves are quarter-turn valves that use a rotating ball to control the flow of a medium. These valves offer fast and efficient control, making them ideal for on-off applications. However, with proper actuation, ball valves can also be used for modulating purposes. The ball's rotation can be adjusted to regulate the flow rate, offering a high level of control. They are commonly used in industries such as chemical processing and water treatment.
Butterfly valves are another type of quarter-turn valve that uses a disc to control the flow. The disc rotates on a central axis to open, close, or partially block the flow. Butterfly valves are often used in large-scale applications where quick operation is necessary. While they are typically used for on-off functions, they can also be employed in modulating applications, particularly in HVAC and water distribution systems.
Diaphragm valves use a flexible diaphragm to control flow. The diaphragm moves up and down to regulate the flow of fluid through the valve. These valves are known for their excellent control capabilities and are often used in applications that require precision, such as pharmaceutical manufacturing or food processing.
Plug valves use a cylindrical or conically tapered plug to control the flow. The plug is rotated within the valve body to modulate the flow. Plug valves are typically used in systems where a high level of control is needed, such as in oil and gas pipelines or chemical processing plants.
Proper maintenance is essential for the reliable operation of modulating control valves. Because these valves are constantly in motion, they are subject to wear and tear. Regular inspection, cleaning, and lubrication are necessary to ensure that the valve continues to function smoothly.
Regular inspection of the valve and actuator is crucial. This includes checking for signs of wear on the valve body, actuator, and seals. Any abnormal noise, vibration, or leakage should be addressed immediately to prevent further damage. Valves should be cleaned regularly to remove any debris or buildup that could interfere with the valve's operation. In some cases, the buildup of sediment or chemicals can affect the valve's ability to modulate flow accurately. Regular cleaning ensures that the valve remains responsive and efficient. Moving parts, especially in mechanical actuators, should be lubricated periodically. This reduces friction and wear, ensuring smooth operation. However, it's essential to use the appropriate lubricant for the specific valve and medium being controlled. Actuators and feedback systems need to be calibrated regularly to ensure that the valve's position accurately reflects the desired flow rate. Over time, calibration can drift, leading to inaccurate control. Regular calibration ensures that the valve operates within its specified parameters. The operation of a modulating control valve involves a combination of mechanical, electrical, and hydraulic components. The actuator is the key component responsible for moving the valve to the desired position. There are several types of actuators, including pneumatic, electric, and hydraulic actuators. Pneumatic actuators use air pressure to move the valve stem and modulate the flow. These actuators are common in industrial applications due to their simplicity and reliability. The position of the valve is controlled by adjusting the air pressure supplied to the actuator. Electric actuators use an electric motor to control the valve's position. They offer precise control and are often used in applications where accuracy is critical. Electric actuators can be integrated with control systems for remote operation and monitoring. Hydraulic actuators use pressurized fluid to control the valve. These actuators are typically used in heavy-duty applications where high force is required. They provide excellent control and are commonly found in industries such as oil and gas.
The feedback system is another critical component of the modulating valve. It provides real-time information on the valve’s position, which is relayed to the operator or control system. This allows for adjustments to be made based on the specific requirements of the process. The combination of an actuator and feedback system enables the modulating control valve to operate with high precision. Modulating control valves play a critical role in a wide range of industrial applications by offering precise control over the flow of fluids. Their ability to adjust to intermediate positions between fully open and fully closed allows for better process control, leading to increased efficiency and reduced operational costs. With proper maintenance, these valves provide reliable performance, ensuring that systems run smoothly and within desired parameters. Whether in heating and cooling systems, chemical processing, or water treatment, modulating control valves are essential for maintaining process stability and efficiency.
Modulating control valves are crucial for maintaining process stability, especially in systems where factors like temperature, pressure, or fluid levels need to be carefully monitored and controlled. The feedback system integrated into these valves communicates with the operator or control system, allowing real-time adjustments to be made. Common modulating control valves include globe valves, disc valves, and quarter-turn valves such as butterfly and ball valves. With their ability to fine-tune flow, these valves are vital to numerous industries including HVAC, chemical processing, and water treatment. Modulation refers to the ability of a valve to adjust its position between fully open and fully closed to regulate the flow of a medium. Unlike conventional valves that only provide an open or closed state, modulating valves control the degree of openness, allowing for a more precise and continuous regulation of flow. This is crucial for processes where the exact flow rate needs to be maintained over time, rather than simply being turned on or off.
Modulating control is often used to manage secondary variables, such as temperature, pressure, or the level of fluid in a tank. For instance, in a heating system, a modulating valve can control the flow of hot water to maintain a specific room temperature. In industrial processes, modulating valves are used to control the flow of chemicals, steam, or gases to ensure precise conditions are met. This fine-tuned control helps improve efficiency, reduce energy consumption, and ensure product quality.
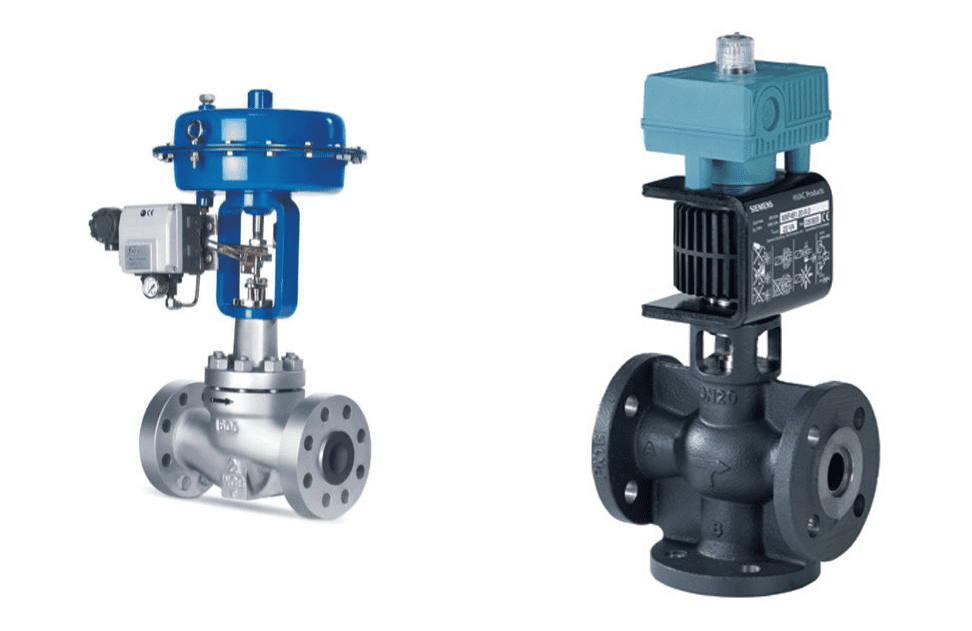
Regular inspection of the valve and actuator is crucial. This includes checking for signs of wear on the valve body, actuator, and seals. Any abnormal noise, vibration, or leakage should be addressed immediately to prevent further damage. Valves should be cleaned regularly to remove any debris or buildup that could interfere with the valve's operation. In some cases, the buildup of sediment or chemicals can affect the valve's ability to modulate flow accurately. Regular cleaning ensures that the valve remains responsive and efficient. Moving parts, especially in mechanical actuators, should be lubricated periodically. This reduces friction and wear, ensuring smooth operation. However, it's essential to use the appropriate lubricant for the specific valve and medium being controlled. Actuators and feedback systems need to be calibrated regularly to ensure that the valve's position accurately reflects the desired flow rate. Over time, calibration can drift, leading to inaccurate control. Regular calibration ensures that the valve operates within its specified parameters. The operation of a modulating control valve involves a combination of mechanical, electrical, and hydraulic components. The actuator is the key component responsible for moving the valve to the desired position. There are several types of actuators, including pneumatic, electric, and hydraulic actuators. Pneumatic actuators use air pressure to move the valve stem and modulate the flow. These actuators are common in industrial applications due to their simplicity and reliability. The position of the valve is controlled by adjusting the air pressure supplied to the actuator. Electric actuators use an electric motor to control the valve's position. They offer precise control and are often used in applications where accuracy is critical. Electric actuators can be integrated with control systems for remote operation and monitoring. Hydraulic actuators use pressurized fluid to control the valve. These actuators are typically used in heavy-duty applications where high force is required. They provide excellent control and are commonly found in industries such as oil and gas.
The feedback system is another critical component of the modulating valve. It provides real-time information on the valve’s position, which is relayed to the operator or control system. This allows for adjustments to be made based on the specific requirements of the process. The combination of an actuator and feedback system enables the modulating control valve to operate with high precision. Modulating control valves play a critical role in a wide range of industrial applications by offering precise control over the flow of fluids. Their ability to adjust to intermediate positions between fully open and fully closed allows for better process control, leading to increased efficiency and reduced operational costs. With proper maintenance, these valves provide reliable performance, ensuring that systems run smoothly and within desired parameters. Whether in heating and cooling systems, chemical processing, or water treatment, modulating control valves are essential for maintaining process stability and efficiency.