Common Faults in Motorized Control Valves Causes and Solutions
On this page
Motorized control valves are critical components in various industrial processes, offering precise control over fluid flow, pressure, and temperature. However, like any mechanical device, they can develop faults that hinder their performance. Understanding these common faults and their underlying causes is essential for maintaining optimal operation and minimizing downtime. This article delves into some of the most prevalent issues encountered with motorized control valves, along with potential solutions to address them.
Description:
Valve sticking occurs when the valve fails to move smoothly between positions. This issue can result in improper flow control, leading to process inefficiencies.
Causes:
Fouling: Accumulation of debris or contaminants in the valve can cause it to stick.
Corrosion: Corrosion of the valve stem or body can hinder smooth movement.
Inadequate Lubrication: Lack of proper lubrication can increase friction, causing the valve to stick.
Solutions:
Regular Cleaning: Implementing routine cleaning schedules can prevent fouling.
Material Selection: Using corrosion-resistant materials for valve components can mitigate corrosion.
Lubrication Maintenance: Ensuring regular lubrication of moving parts can reduce friction. Description:
The actuator is responsible for moving the valve to its desired position. Actuator failure can prevent the valve from opening or closing as needed.
Causes:
Electrical Issues: Problems with wiring, connectors, or power supply can lead to actuator malfunction.
Mechanical Wear: Over time, components within the actuator can wear out, leading to failure.
Overheating: Excessive heat can damage the actuator’s internal components.
Solutions:
Electrical Inspection: Regularly inspect and maintain electrical connections and power supplies.
Component Replacement: Replace worn-out mechanical parts to maintain actuator performance.
Temperature Control: Implement cooling measures to prevent overheating. Description:
Positioners ensure that the valve reaches the correct position as dictated by the control signal. Malfunctioning positioners can cause inaccurate valve positioning.
Causes:
Calibration Drift: Over time, positioners may drift out of calibration, leading to incorrect positioning.
Signal Interference: Electrical noise or signal interference can disrupt positioner operation.
Mechanical Issues: Internal mechanical faults can impede positioner function.
Solutions:
Regular Calibration: Periodically calibrate positioners to maintain accuracy.
Shielding and Filtering: Use shielding and filtering techniques to minimize signal interference.
Mechanical Inspection: Regularly inspect and maintain mechanical components within the positioner. Description:
Seal leaks occur when the valve fails to completely stop the flow of fluid, resulting in leakage. This can compromise process efficiency and safety.
Causes:
Seal Wear: Over time, seals can wear out or degrade, leading to leaks.
Improper Installation: Incorrect installation of seals can result in gaps or misalignment.
Pressure Fluctuations: Frequent or extreme pressure changes can damage seals.
Solutions:
Seal Replacement: Regularly replace worn or damaged seals to prevent leaks.
Proper Installation: Ensure seals are installed correctly according to manufacturer guidelines.
Pressure Regulation: Maintain stable pressure conditions to prolong seal life. Description:
Hysteresis refers to the lag between the input signal and the valve's actual position. High hysteresis can lead to control inaccuracies.
Causes:
Friction: Excessive friction within the valve mechanism can cause hysteresis.
Backlash: Mechanical play or looseness can contribute to hysteresis.
Control Loop Issues: Improper tuning of the control loop can exacerbate hysteresis.
Solutions:
Friction Reduction: Regular lubrication and maintenance can minimize friction.
Precision Components: Use high-precision components to reduce backlash.
Control Loop Tuning: Properly tune the control loop to enhance response accuracy. Description:
Excessive noise and vibration in motorized control valves can indicate underlying issues and may lead to mechanical damage over time.
Causes:
Cavitation: Rapid pressure changes can cause cavitation, leading to noise and vibration.
Flow Turbulence: Irregular fluid flow patterns can generate noise and vibration.
Component Misalignment: Misaligned components can exacerbate noise and vibration.
Solutions:
Cavitation Control: Implement measures to control pressure changes and prevent cavitation.
Flow Management: Design the system to ensure smooth and stable fluid flow.
Alignment Checks: Regularly inspect and correct any misalignments in the valve assembly. Motorized control valves are indispensable for precise process control in various industries. By understanding and addressing common faults such as valve sticking, actuator failure, positioner malfunction, seal leaks, hysteresis, and noise and vibration, operators can enhance valve performance, reduce downtime, and maintain efficient operations. Regular maintenance, proper installation, and proactive measures are key to preventing these issues and ensuring reliable valve function.
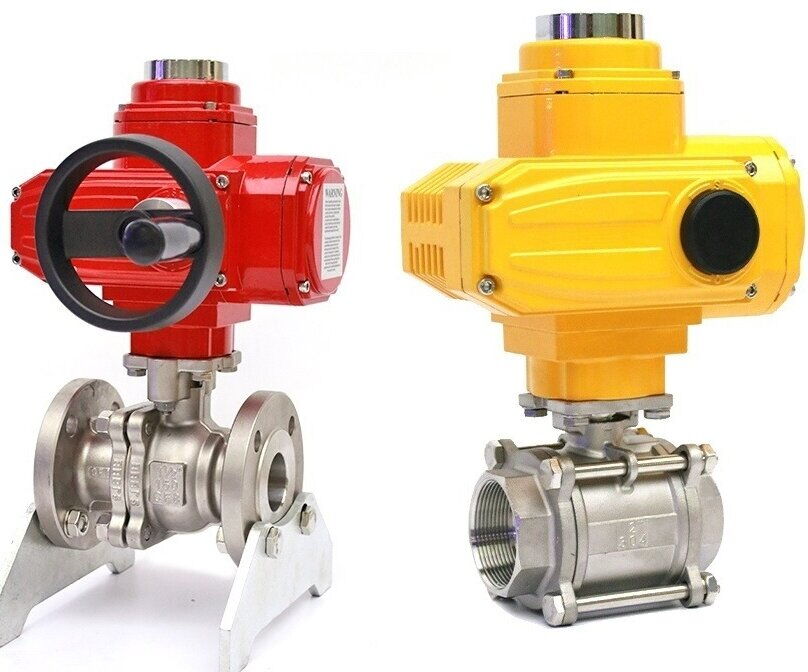
Motorized Control Valves
Description:
Valve sticking occurs when the valve fails to move smoothly between positions. This issue can result in improper flow control, leading to process inefficiencies.
Causes:
Fouling: Accumulation of debris or contaminants in the valve can cause it to stick.
Corrosion: Corrosion of the valve stem or body can hinder smooth movement.
Inadequate Lubrication: Lack of proper lubrication can increase friction, causing the valve to stick.
Solutions:
Regular Cleaning: Implementing routine cleaning schedules can prevent fouling.
Material Selection: Using corrosion-resistant materials for valve components can mitigate corrosion.
Lubrication Maintenance: Ensuring regular lubrication of moving parts can reduce friction. Description:
The actuator is responsible for moving the valve to its desired position. Actuator failure can prevent the valve from opening or closing as needed.
Causes:
Electrical Issues: Problems with wiring, connectors, or power supply can lead to actuator malfunction.
Mechanical Wear: Over time, components within the actuator can wear out, leading to failure.
Overheating: Excessive heat can damage the actuator’s internal components.
Solutions:
Electrical Inspection: Regularly inspect and maintain electrical connections and power supplies.
Component Replacement: Replace worn-out mechanical parts to maintain actuator performance.
Temperature Control: Implement cooling measures to prevent overheating. Description:
Positioners ensure that the valve reaches the correct position as dictated by the control signal. Malfunctioning positioners can cause inaccurate valve positioning.
Causes:
Calibration Drift: Over time, positioners may drift out of calibration, leading to incorrect positioning.
Signal Interference: Electrical noise or signal interference can disrupt positioner operation.
Mechanical Issues: Internal mechanical faults can impede positioner function.
Solutions:
Regular Calibration: Periodically calibrate positioners to maintain accuracy.
Shielding and Filtering: Use shielding and filtering techniques to minimize signal interference.
Mechanical Inspection: Regularly inspect and maintain mechanical components within the positioner. Description:
Seal leaks occur when the valve fails to completely stop the flow of fluid, resulting in leakage. This can compromise process efficiency and safety.
Causes:
Seal Wear: Over time, seals can wear out or degrade, leading to leaks.
Improper Installation: Incorrect installation of seals can result in gaps or misalignment.
Pressure Fluctuations: Frequent or extreme pressure changes can damage seals.
Solutions:
Seal Replacement: Regularly replace worn or damaged seals to prevent leaks.
Proper Installation: Ensure seals are installed correctly according to manufacturer guidelines.
Pressure Regulation: Maintain stable pressure conditions to prolong seal life. Description:
Hysteresis refers to the lag between the input signal and the valve's actual position. High hysteresis can lead to control inaccuracies.
Causes:
Friction: Excessive friction within the valve mechanism can cause hysteresis.
Backlash: Mechanical play or looseness can contribute to hysteresis.
Control Loop Issues: Improper tuning of the control loop can exacerbate hysteresis.
Solutions:
Friction Reduction: Regular lubrication and maintenance can minimize friction.
Precision Components: Use high-precision components to reduce backlash.
Control Loop Tuning: Properly tune the control loop to enhance response accuracy. Description:
Excessive noise and vibration in motorized control valves can indicate underlying issues and may lead to mechanical damage over time.
Causes:
Cavitation: Rapid pressure changes can cause cavitation, leading to noise and vibration.
Flow Turbulence: Irregular fluid flow patterns can generate noise and vibration.
Component Misalignment: Misaligned components can exacerbate noise and vibration.
Solutions:
Cavitation Control: Implement measures to control pressure changes and prevent cavitation.
Flow Management: Design the system to ensure smooth and stable fluid flow.
Alignment Checks: Regularly inspect and correct any misalignments in the valve assembly. Motorized control valves are indispensable for precise process control in various industries. By understanding and addressing common faults such as valve sticking, actuator failure, positioner malfunction, seal leaks, hysteresis, and noise and vibration, operators can enhance valve performance, reduce downtime, and maintain efficient operations. Regular maintenance, proper installation, and proactive measures are key to preventing these issues and ensuring reliable valve function.