How to Size a Control Valve?
On this page
Choosing the correct size for a control valve is critical to the efficiency, safety, and longevity of any industrial process system. An improperly sized valve can lead to operational inefficiencies, increased maintenance costs, and potential safety hazards. Here’s a comprehensive guide on how to consider the size of a control valve, covering key factors and steps in the sizing process.
Control valve sizing is the process of determining the appropriate valve size to ensure optimal flow control in a system. The main objective is to match the valve’s flow characteristics with the requirements of the process, ensuring that the valve operates within its optimal range. Several factors influence the sizing of a control valve: The amount of fluid that needs to pass through the valve per unit of time is a fundamental consideration. It’s essential to know the maximum and minimum flow rates to ensure the valve can handle the full range of operating conditions. The pressure difference between the valve’s inlet and outlet is crucial for determining the valve size. An excessive pressure drop can lead to inefficiency and increased wear, while too little can result in poor control. The type of fluid (liquid, gas, or steam) and its properties, such as viscosity, density, and temperature, significantly impact the valve selection. These characteristics affect the flow dynamics and must be considered in the sizing process.
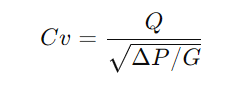
where:
Q is the flow rate,
ΔP is the pressure drop,
G is the specific gravity of the fluid.
Different formulas and correction factors are used for liquids, gases, and steam. Based on the calculated Cv and the process requirements, choose the appropriate valve type and size. Manufacturers provide Cv charts for their valves, which help in selecting a valve that meets the desired flow characteristics. Ensure that the selected valve can operate effectively within the full range of process conditions. This includes verifying that the valve can handle the maximum flow rate and maintain control at low flow rates without excessive pressure drop. Evaluate the valve’s performance in terms of safety and ease of maintenance. A well-sized valve should minimize the risk of cavitation, flashing, and excessive noise, which can lead to damage and require frequent maintenance. Use simulation tools to model the valve’s performance within the system. This step helps in identifying potential issues and ensuring that the valve will function as expected under various operating scenarios. Oversizing: A common mistake is selecting a valve that is too large, which can result in poor control and increased wear. An oversized valve operates mostly in a partially open position, leading to instability and noise.
Undersizing: Choosing a valve that is too small can cause high-pressure drops, reduced flow capacity, and potential system failures. It’s crucial to balance the valve size to match the process needs accurately.
Ignoring Fluid Dynamics: Failing to consider the specific properties of the fluid can lead to incorrect sizing. Always account for viscosity, density, and temperature variations in the sizing calculations. Proper control valve sizing is essential for efficient and reliable operation of industrial systems. By considering flow rates, pressure drops, fluid characteristics, and system dynamics, and by following a structured sizing process, you can ensure that the selected valve will perform optimally. Avoiding common pitfalls and using simulation tools can further enhance the accuracy of valve sizing, leading to improved process control and reduced maintenance costs.
Control valve sizing is the process of determining the appropriate valve size to ensure optimal flow control in a system. The main objective is to match the valve’s flow characteristics with the requirements of the process, ensuring that the valve operates within its optimal range. Several factors influence the sizing of a control valve: The amount of fluid that needs to pass through the valve per unit of time is a fundamental consideration. It’s essential to know the maximum and minimum flow rates to ensure the valve can handle the full range of operating conditions. The pressure difference between the valve’s inlet and outlet is crucial for determining the valve size. An excessive pressure drop can lead to inefficiency and increased wear, while too little can result in poor control. The type of fluid (liquid, gas, or steam) and its properties, such as viscosity, density, and temperature, significantly impact the valve selection. These characteristics affect the flow dynamics and must be considered in the sizing process.
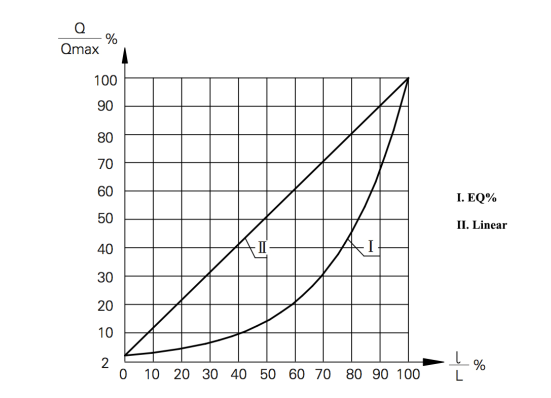
Flow Characteristics
Different valve types, such as globe, butterfly, or ball valves, have unique flow characteristics and capacities. Selecting the appropriate valve type based on the specific application is vital.
Understanding the overall system dynamics, including the interaction between various components and potential variations in operating conditions, helps in choosing a valve that can maintain stable control.
Gather all relevant data about the process, including flow rates, pressure conditions, fluid properties, and temperature ranges. This information forms the foundation for the sizing calculations.
The flow coefficient, Cv, is a key parameter in valve sizing, representing the flow capacity of the valve. It indicates how much fluid can pass through the valve with a specific pressure drop. The Cv is calculated using the formula: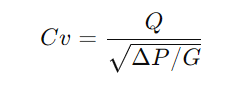
where:
Q is the flow rate,
ΔP is the pressure drop,
G is the specific gravity of the fluid.
Different formulas and correction factors are used for liquids, gases, and steam. Based on the calculated Cv and the process requirements, choose the appropriate valve type and size. Manufacturers provide Cv charts for their valves, which help in selecting a valve that meets the desired flow characteristics. Ensure that the selected valve can operate effectively within the full range of process conditions. This includes verifying that the valve can handle the maximum flow rate and maintain control at low flow rates without excessive pressure drop. Evaluate the valve’s performance in terms of safety and ease of maintenance. A well-sized valve should minimize the risk of cavitation, flashing, and excessive noise, which can lead to damage and require frequent maintenance. Use simulation tools to model the valve’s performance within the system. This step helps in identifying potential issues and ensuring that the valve will function as expected under various operating scenarios. Oversizing: A common mistake is selecting a valve that is too large, which can result in poor control and increased wear. An oversized valve operates mostly in a partially open position, leading to instability and noise.
Undersizing: Choosing a valve that is too small can cause high-pressure drops, reduced flow capacity, and potential system failures. It’s crucial to balance the valve size to match the process needs accurately.
Ignoring Fluid Dynamics: Failing to consider the specific properties of the fluid can lead to incorrect sizing. Always account for viscosity, density, and temperature variations in the sizing calculations. Proper control valve sizing is essential for efficient and reliable operation of industrial systems. By considering flow rates, pressure drops, fluid characteristics, and system dynamics, and by following a structured sizing process, you can ensure that the selected valve will perform optimally. Avoiding common pitfalls and using simulation tools can further enhance the accuracy of valve sizing, leading to improved process control and reduced maintenance costs.