How Control Valves Work?
On this page
Control valves are pivotal components in industrial processes, responsible for regulating the flow of fluids, gases, or slurries within a system. By precisely adjusting the flow rate, control valves help maintain the desired process conditions, ensuring optimal performance and safety. This article delves into the mechanics of how control valves work, highlighting their types, components, and operational principles.
At the heart of every control valve lies several key components: The main structure that houses the internal components and directs the flow of the fluid. The device that moves the valve stem or plug, which can be powered pneumatically, electrically, or hydraulically. Connects the actuator to the valve plug or disc, transmitting the motion needed to open or close the valve. The part that moves to adjust the flow passage within the valve body. The surface against which the valve plug seals to shut off flow. A device that ensures the valve achieves the desired degree of opening by comparing the control signal with the valve position and making necessary adjustments.
Control valves operate by adjusting the position of the valve plug within the valve body to modulate flow. This process can be broken down into several steps: The control valve receives a signal from a process controller, indicating the desired flow rate. This signal can be pneumatic (3-15 psi), electric (4-20 mA), or digital. The actuator responds to the control signal by moving the valve stem.Pneumatic actuators use air pressure, electric actuators use motors, and hydraulic actuators use fluid pressure to create movement. As the actuator moves the valve stem, the valve plug or disc changes its position relative to the seat. This adjustment alters the size of the flow passage, thereby controlling the flow rate of the fluid through the valve. The positioner monitors the valve stem's position and provides feedback to the actuator to ensure the valve achieves the desired position accurately. This feedback loop helps maintain precise control over the process conditions.
Control valves come in various types, each suited for specific applications and operating conditions: Known for their precise throttling capabilities, globe valves are ideal for applications requiring fine control over flow rates. They feature a spherical body and a movable plug that regulates flow. Featuring a rotatable ball with a hole through its center, ball valves are excellent for quick shut-off applications. When the ball is rotated, the hole aligns or misaligns with the flow passage, controlling the flow. Characterized by a rotating disc, butterfly valves are used for large volume flows and lower pressure applications. The disc's rotation adjusts the flow passage. Utilizing a flexible diaphragm to regulate flow, these valves are suitable for handling corrosive or viscous fluids. Typically used for on/off control rather than throttling, gate valves employ a sliding gate to block or allow flow.
Control valves are indispensable in various industries, including oil and gas, chemical processing, water treatment, and power generation. They play a crucial role in maintaining process efficiency, safety, and product quality by ensuring precise control over fluid flow and pressure.
For example, in a chemical processing plant, control valves regulate the flow of reactants to ensure optimal reaction conditions, directly impacting the yield and quality of the final product. In water treatment facilities, control valves manage the flow of water and chemicals to maintain proper treatment levels and ensure safe drinking water.
Control valves are complex yet essential devices that enable precise regulation of fluid flow within industrial systems. Understanding their components, operational mechanisms, and types is crucial for optimizing process control and ensuring the safe and efficient operation of industrial processes. By maintaining the correct flow rates and pressures, control valves help achieve desired process outcomes and enhance overall system performance.
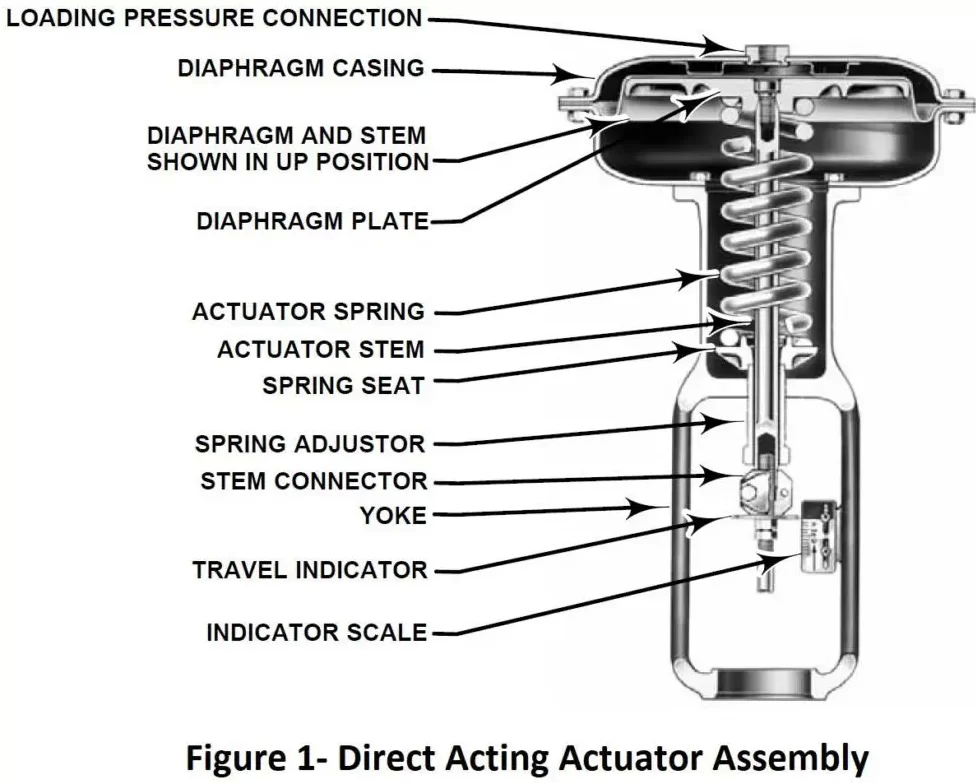
At the heart of every control valve lies several key components: The main structure that houses the internal components and directs the flow of the fluid. The device that moves the valve stem or plug, which can be powered pneumatically, electrically, or hydraulically. Connects the actuator to the valve plug or disc, transmitting the motion needed to open or close the valve. The part that moves to adjust the flow passage within the valve body. The surface against which the valve plug seals to shut off flow. A device that ensures the valve achieves the desired degree of opening by comparing the control signal with the valve position and making necessary adjustments.
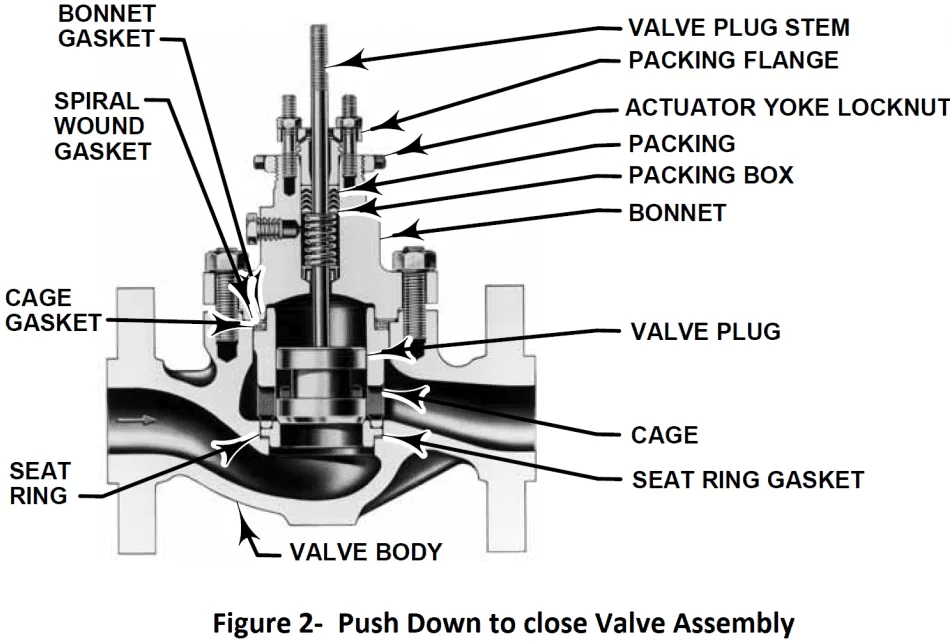
Control valves operate by adjusting the position of the valve plug within the valve body to modulate flow. This process can be broken down into several steps: The control valve receives a signal from a process controller, indicating the desired flow rate. This signal can be pneumatic (3-15 psi), electric (4-20 mA), or digital. The actuator responds to the control signal by moving the valve stem.Pneumatic actuators use air pressure, electric actuators use motors, and hydraulic actuators use fluid pressure to create movement. As the actuator moves the valve stem, the valve plug or disc changes its position relative to the seat. This adjustment alters the size of the flow passage, thereby controlling the flow rate of the fluid through the valve. The positioner monitors the valve stem's position and provides feedback to the actuator to ensure the valve achieves the desired position accurately. This feedback loop helps maintain precise control over the process conditions.
Control valves come in various types, each suited for specific applications and operating conditions: Known for their precise throttling capabilities, globe valves are ideal for applications requiring fine control over flow rates. They feature a spherical body and a movable plug that regulates flow. Featuring a rotatable ball with a hole through its center, ball valves are excellent for quick shut-off applications. When the ball is rotated, the hole aligns or misaligns with the flow passage, controlling the flow. Characterized by a rotating disc, butterfly valves are used for large volume flows and lower pressure applications. The disc's rotation adjusts the flow passage. Utilizing a flexible diaphragm to regulate flow, these valves are suitable for handling corrosive or viscous fluids. Typically used for on/off control rather than throttling, gate valves employ a sliding gate to block or allow flow.
Control valves are indispensable in various industries, including oil and gas, chemical processing, water treatment, and power generation. They play a crucial role in maintaining process efficiency, safety, and product quality by ensuring precise control over fluid flow and pressure.
For example, in a chemical processing plant, control valves regulate the flow of reactants to ensure optimal reaction conditions, directly impacting the yield and quality of the final product. In water treatment facilities, control valves manage the flow of water and chemicals to maintain proper treatment levels and ensure safe drinking water.
Control valves are complex yet essential devices that enable precise regulation of fluid flow within industrial systems. Understanding their components, operational mechanisms, and types is crucial for optimizing process control and ensuring the safe and efficient operation of industrial processes. By maintaining the correct flow rates and pressures, control valves help achieve desired process outcomes and enhance overall system performance.