How Does a Pneumatic Control Valve Work?
On this page
Pneumatic control valves play a crucial role in various industrial processes, regulating the flow of gases, liquids, and other media through pipelines. These valves, powered by compressed air, provide precise control over the flow and pressure, ensuring efficient and safe operation of complex systems. Understanding how pneumatic control valves work can illuminate their importance in sectors such as manufacturing, chemical processing, and energy production.
At its core, a pneumatic control valve consists of three main components: the valve body, the actuator, and the positioner. This is the part through which the fluid flows. It includes the inlet and outlet ports, and a mechanism to open, close, or partially obstruct the flow path. Common types of valve bodies include globe, butterfly, and ball valves. The actuator is the muscle of the valve, converting the energy from the compressed air into mechanical motion. This motion moves the valve plug, ball, or disc to regulate the flow. Actuators can be single-acting or double-acting:
Single-Acting Actuators rely on air pressure for movement in one direction and a spring for the return.
Double-Acting Actuators use air pressure for movement in both directions, allowing for greater control precision. This component ensures the valve achieves the desired degree of openness. It receives a control signal (often from a central control system), compares it to the actual valve position, and adjusts the actuator accordingly to match the target position. This feedback loop is essential for maintaining accurate flow control. The process begins with the control system sending a signal to the valve positioner. This signal typically ranges from 4 to 20 mA in current or 3 to 15 psi in pressure. The positioner interprets the control signal, determining the desired valve position. If the valve's current position differs from the desired position, the positioner sends a pneumatic signal to the actuator. The actuator, responding to the pneumatic signal, moves the valve stem. In single-acting actuators, air pressure pushes the valve in one direction, while a spring returns it to its original position. In double-acting actuators, air pressure can move the valve in both directions, providing more precise control. The movement of the actuator translates into the motion of the valve plug, disc, or ball, adjusting the flow path through the valve body. The valve can fully open, fully close, or maintain any intermediate position to regulate the flow according to the process requirements. The positioner continuously monitors the valve's position, ensuring it matches the control signal. If there is any deviation, the positioner corrects it by adjusting the actuator, maintaining the desired flow rate and pressure.
Pneumatic control valves are employed across a range of industries due to their reliability, durability, and efficiency. They are particularly valued in environments where electrical actuators might pose a hazard, such as in flammable or explosive atmospheres.
Manufacturing: In manufacturing, these valves control the flow of materials, ensuring consistent quality and efficiency in production lines.
Chemical Processing: Pneumatic valves manage the flow of chemicals, maintaining precise conditions necessary for reactions and product quality.
Energy Production: In power plants and refineries, they regulate steam, gas, and other fluids, optimizing energy production and minimizing waste.
The benefits of pneumatic control valves include:
Precision: The feedback loop between the positioner and the actuator allows for exact control over flow rates and pressure.
Safety: By avoiding electrical components, pneumatic valves reduce the risk of sparks and fires in hazardous environments.
Durability: These valves are robust and can withstand harsh conditions, including high pressures and extreme temperatures.
Pneumatic control valves are indispensable components in modern industrial processes. Their ability to provide precise and reliable control over fluid flow makes them essential in various applications. Understanding their operation helps in appreciating their role in enhancing efficiency, safety, and productivity across multiple sectors.
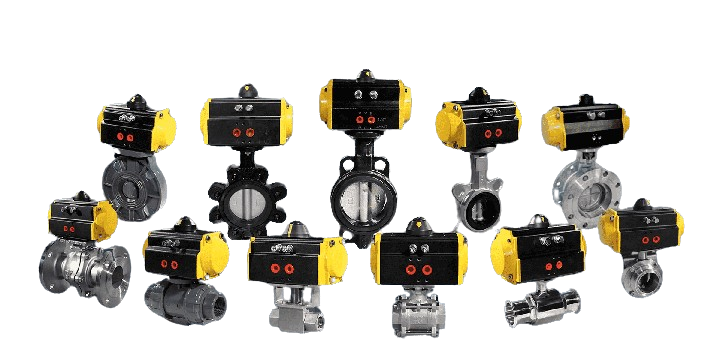
Pneumatic Control Valves
At its core, a pneumatic control valve consists of three main components: the valve body, the actuator, and the positioner. This is the part through which the fluid flows. It includes the inlet and outlet ports, and a mechanism to open, close, or partially obstruct the flow path. Common types of valve bodies include globe, butterfly, and ball valves. The actuator is the muscle of the valve, converting the energy from the compressed air into mechanical motion. This motion moves the valve plug, ball, or disc to regulate the flow. Actuators can be single-acting or double-acting:
Single-Acting Actuators rely on air pressure for movement in one direction and a spring for the return.
Double-Acting Actuators use air pressure for movement in both directions, allowing for greater control precision. This component ensures the valve achieves the desired degree of openness. It receives a control signal (often from a central control system), compares it to the actual valve position, and adjusts the actuator accordingly to match the target position. This feedback loop is essential for maintaining accurate flow control. The process begins with the control system sending a signal to the valve positioner. This signal typically ranges from 4 to 20 mA in current or 3 to 15 psi in pressure. The positioner interprets the control signal, determining the desired valve position. If the valve's current position differs from the desired position, the positioner sends a pneumatic signal to the actuator. The actuator, responding to the pneumatic signal, moves the valve stem. In single-acting actuators, air pressure pushes the valve in one direction, while a spring returns it to its original position. In double-acting actuators, air pressure can move the valve in both directions, providing more precise control. The movement of the actuator translates into the motion of the valve plug, disc, or ball, adjusting the flow path through the valve body. The valve can fully open, fully close, or maintain any intermediate position to regulate the flow according to the process requirements. The positioner continuously monitors the valve's position, ensuring it matches the control signal. If there is any deviation, the positioner corrects it by adjusting the actuator, maintaining the desired flow rate and pressure.
Pneumatic control valves are employed across a range of industries due to their reliability, durability, and efficiency. They are particularly valued in environments where electrical actuators might pose a hazard, such as in flammable or explosive atmospheres.
Manufacturing: In manufacturing, these valves control the flow of materials, ensuring consistent quality and efficiency in production lines.
Chemical Processing: Pneumatic valves manage the flow of chemicals, maintaining precise conditions necessary for reactions and product quality.
Energy Production: In power plants and refineries, they regulate steam, gas, and other fluids, optimizing energy production and minimizing waste.
The benefits of pneumatic control valves include:
Precision: The feedback loop between the positioner and the actuator allows for exact control over flow rates and pressure.
Safety: By avoiding electrical components, pneumatic valves reduce the risk of sparks and fires in hazardous environments.
Durability: These valves are robust and can withstand harsh conditions, including high pressures and extreme temperatures.
Pneumatic control valves are indispensable components in modern industrial processes. Their ability to provide precise and reliable control over fluid flow makes them essential in various applications. Understanding their operation helps in appreciating their role in enhancing efficiency, safety, and productivity across multiple sectors.